Six Sigma Success: Boost Productivity and Quality
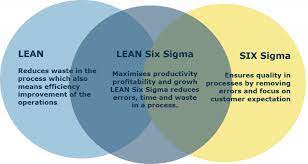
In the world of business and process improvement, Six Sigma stands as a beacon of excellence. Originating from Motorola in the 1980s and later perfected by General Electric, this data-driven methodology has become synonymous with quality and efficiency. In this blog, we’ll explore the principles, tools, and benefits of Six Sigma, providing you with valuable insights into how it can transform your organization.
Chapter 1: Understanding Six Sigma
What is Six Sigma?
Six Sigma is a systematic approach to process improvement that aims to minimize defects and variations while maximizing efficiency and quality. It achieves this by relying on data, statistical analysis, and a structured problem-solving methodology.
Key Concepts of Six Sigma
- DMAIC: Define, Measure, Analyze, Improve, and Control – the five phases of Six Sigma.
- Roles: Green Belts, Black Belts, and Master Black Belts are individuals trained in Six Sigma methodology to lead improvement projects.
- Metrics: Six Sigma uses critical metrics like DPMO (Defects Per Million Opportunities) to measure process performance.
Chapter 2: The DMAIC Process
Define Phase
In this phase, you identify the problem, set project goals, and define customer requirements. It’s essential to have a clear understanding of what needs improvement before proceeding.
Measure Phase
This phase involves gathering data on the current process, determining its performance, and identifying potential causes of defects. Data collection and analysis are critical here.
Analyze Phase
Here, you dig deeper into the data to understand the root causes of defects. Tools like Fishbone diagrams and Pareto charts can be invaluable in this phase.
Improve Phase
Once you’ve identified the root causes, you work on implementing improvements. This phase involves designing and testing solutions to eliminate defects and improve the process.
Control Phase
In the final phase, you establish controls to ensure the improvements are sustained over time. This includes developing monitoring systems and training staff to follow the new process.
Chapter 3: The Benefits of Six Sigma
Improved Quality
Six Sigma focuses on reducing defects, leading to higher product and service quality, which, in turn, boosts customer satisfaction.
Increased Efficiency
By optimizing processes, Six Sigma can lead to cost reductions, shorter cycle times, and improved resource utilization.
Data-Driven Decision Making
Six Sigma relies heavily on data and statistics, helping organizations make informed decisions rather than relying on intuition.
Competitive Advantage
Organizations that adopt Six Sigma gain a competitive edge in the market by consistently delivering high-quality products or services.
Chapter 4: Six Sigma Success Stories
General Electric (GE)
GE famously saved billions of dollars by implementing Six Sigma across its operations, proving the methodology’s effectiveness on a large scale.
Motorola
Motorola is where Six Sigma originated. Its success with the methodology set the stage for its widespread adoption in various industries.
Ford Motor Company
Ford turned to Six Sigma to improve vehicle quality and customer satisfaction, leading to significant improvements in its market position.
Chapter 5: Getting Started with Six Sigma
Training and Certification
Consider sending key personnel for Six Sigma training and certification to build the necessary skills and knowledge.
Project Selection
Identify projects that have a significant impact on your organization’s goals and customer satisfaction.
Establishing a Six Sigma Culture
To ensure long-term success, integrate Six Sigma principles into your organization’s culture, encouraging continuous improvement.